
FUJARA – BEHIND THE SCENES
EVERYTHING BEGINS WITH AN IDEA
People see most of the bike customization projects only when they are finished. They can hardy imagine the work and effort behind the built. Fujara was the most complex project we have ever done, involving many different people from various professions. It took over 600 hours to built. But it all paid off. And it all started with a single idea.
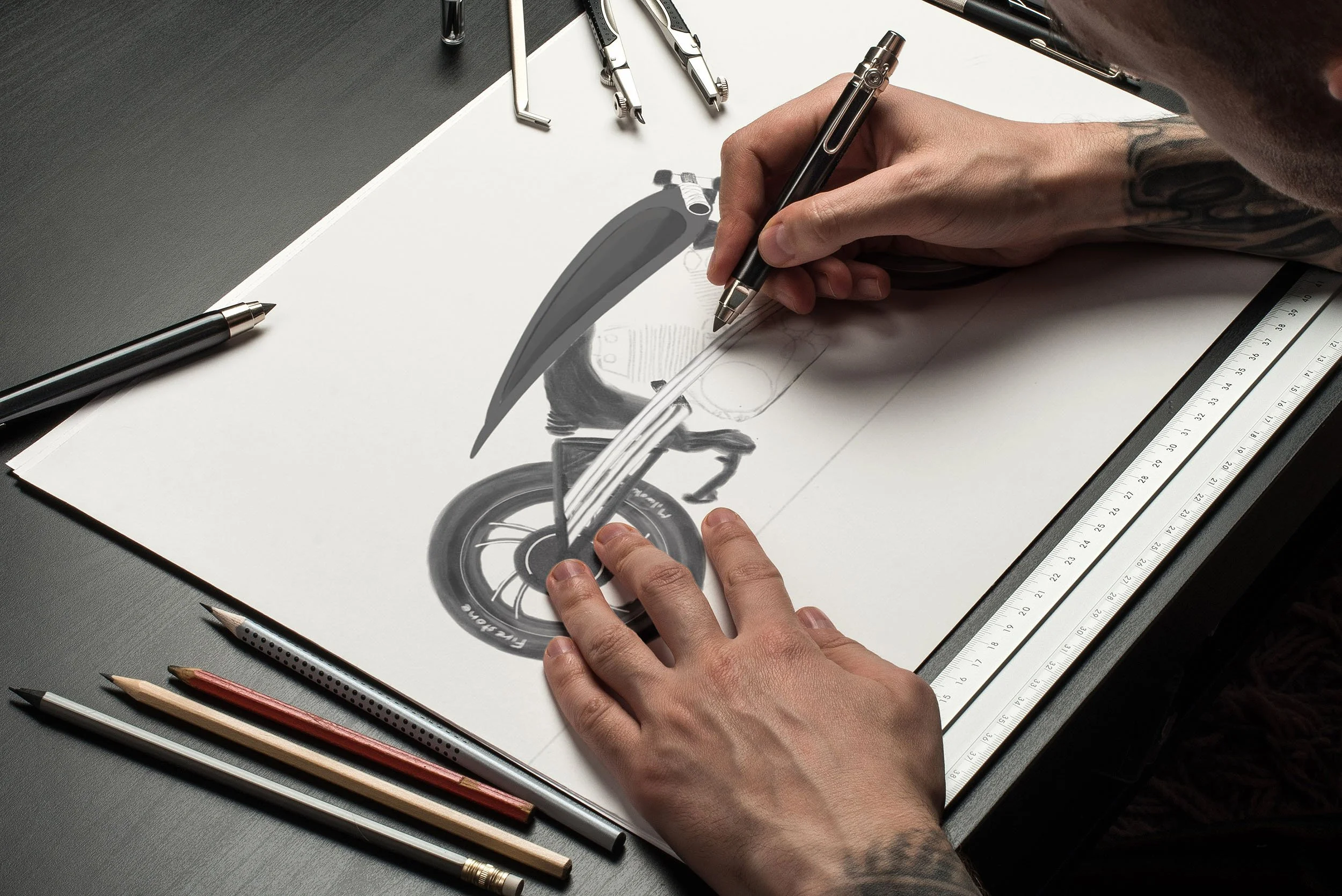
Back in 2017, Earth motorcycles approached an industrial designer Konstantin Laskov from Sofia, Bulgaria to design a unique bike, based on Yamaha XV920. The V-twin mounted from above, giving the engine somewhat levitating feel, together with the curved frame, indicated a great design potential.
The design brief to Konstantin was to come with a subtle shape, contrasting with the big engine, respecting the mentioned core of the bike – the floating engine and the curved frame. On philosophical level, the request was to follow three keywords – freedom, wind and air. Konstantin came with tons of sketches and finally delivered a simple idea of a single tight curve with a peak above the engine and two tangents with the wheels. This became our design mantra.
Hundreds of sketches followed. Almost invisible differences were taken into consideration. And then, after few months of designing, we came to the final shape. The shape of a wing on wheels.
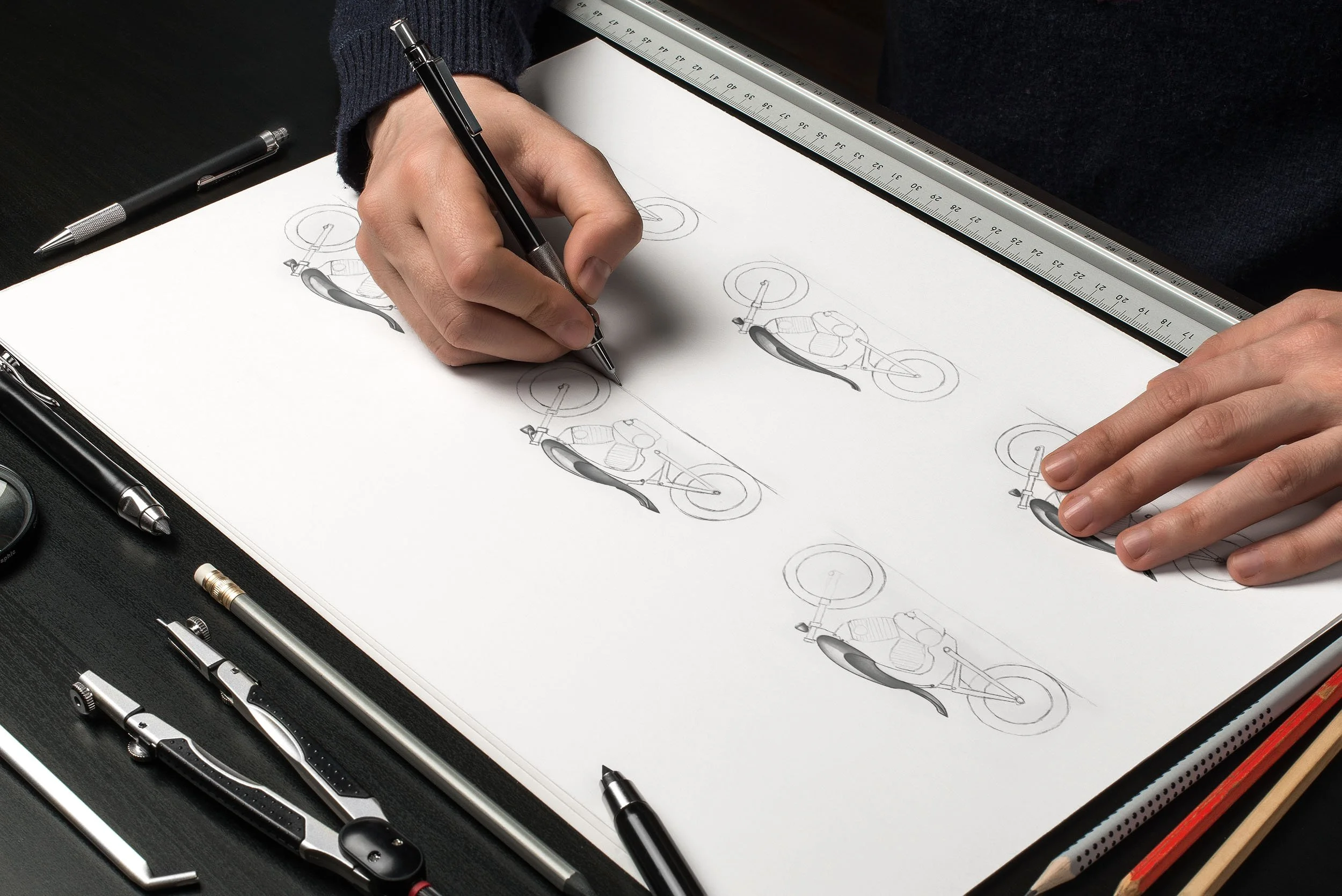

The project Fujara required a 3D model of the entire motorcycle. Of course, it was not possible to buy or obtain a technically accurate 3D model of a bike made in 1984. So, it was necessary to scan the frame with an industrial scanner, and only then, the creation in 3D could begin.
Konstantin remodeled the scanned bike, so that we could see a clean render, once he finished the design. He modelled every single fitting, every screw, every custom part. That allowed us to go on with fabrication of custom parts.
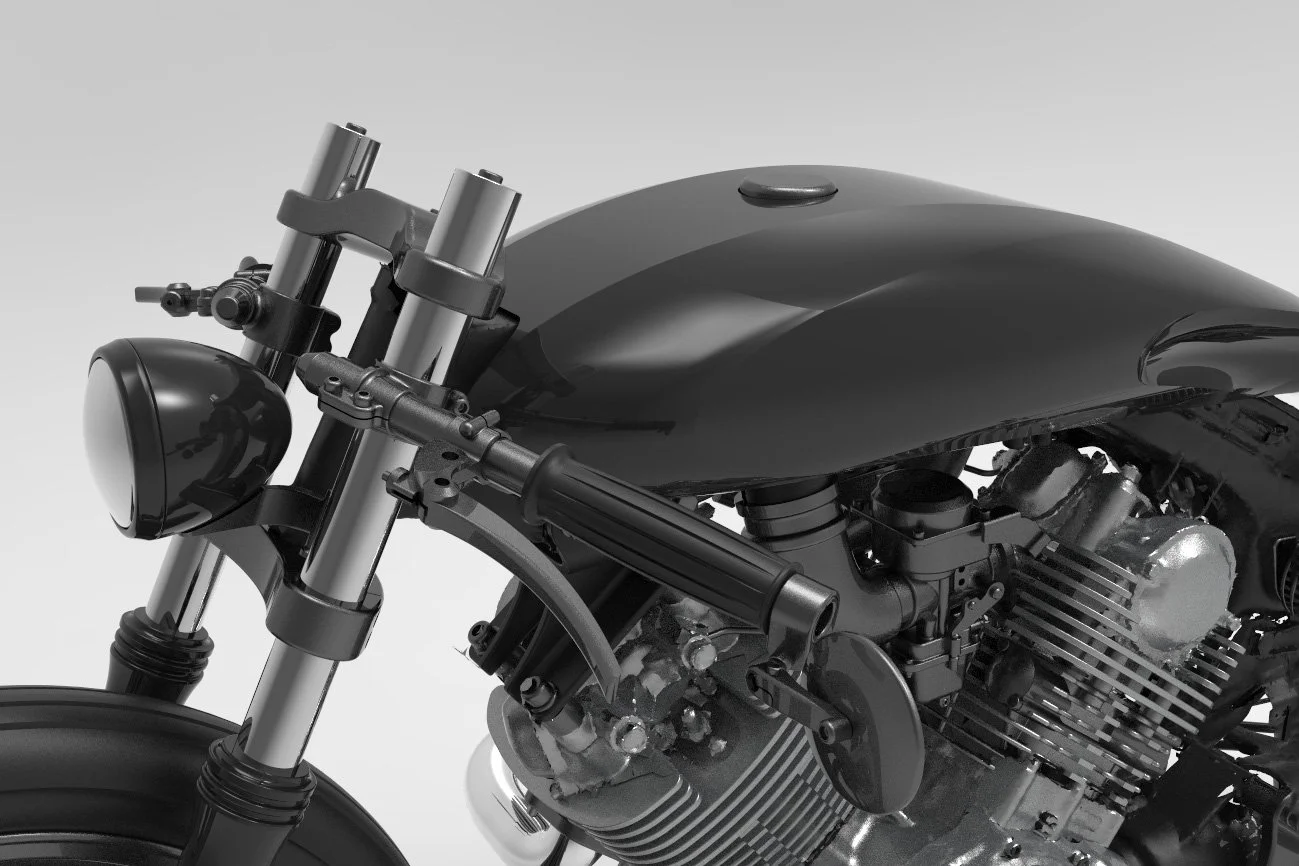
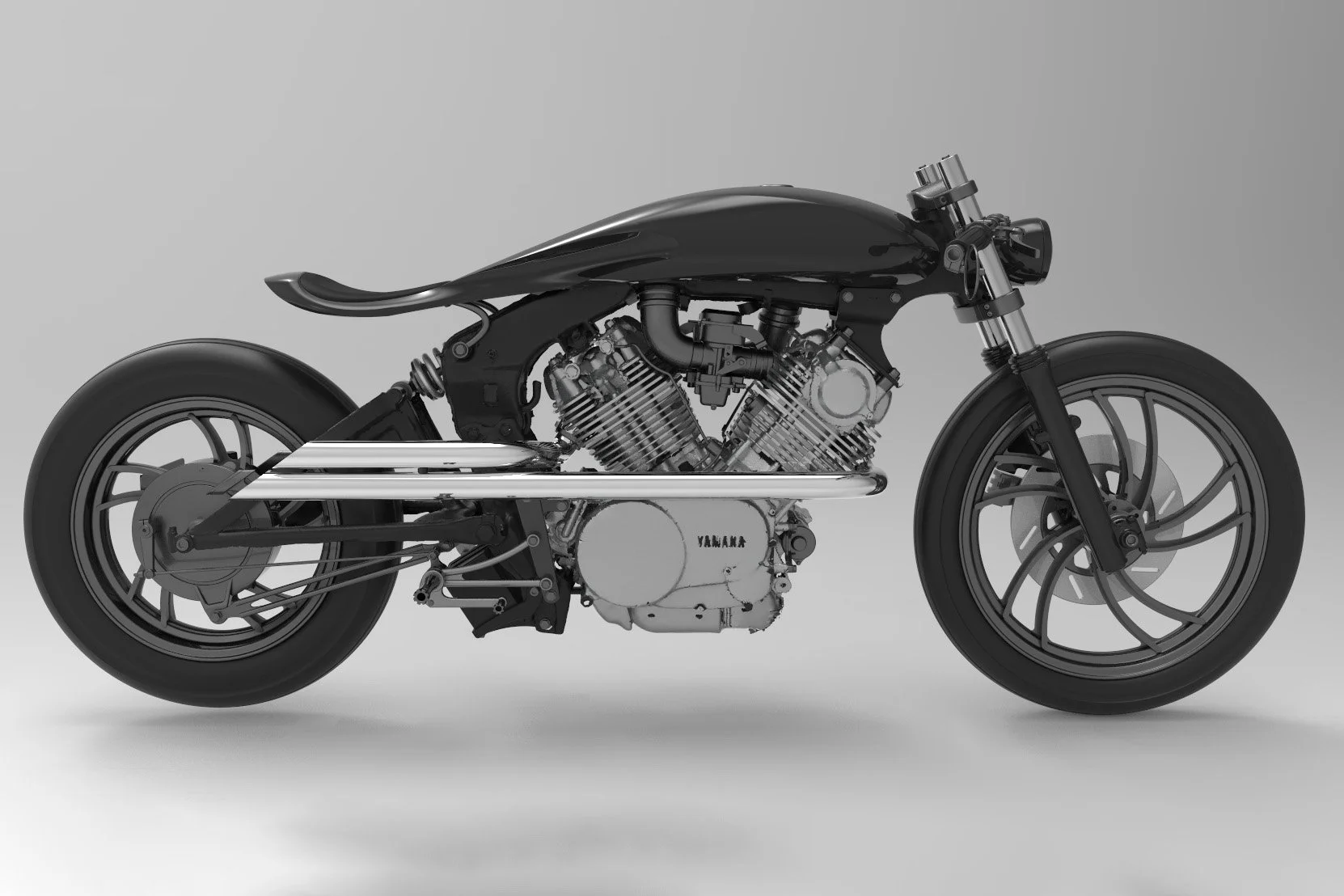
The trickiest part of the bike, technical wise, was the cockpit. We were looking for the most suitable repeatable technology – from milling, thru casting, 3D printing, to a final technology, which was fiberglass molding.
The very first step was a 3D-printed pre-production tank. The problem, however, was that there was no such a 3D printer able to print such a long piece at once. So, it had to be divided in 4 pieces, printed individually and then glued together. This first sample allowed us to test whether the frame was not limiting us somewhere, as well as whether the monocoque fitted ergonomically and visually with the bike.
After several iterations, we made a positive wooden mold first, serving as a base for a final negative mold. Then, we were ready to make the cockpit.

The cockpit was made of special fiber glass and epoxy, resistant to gasoline. The layers of fiber glass had to be laid down in a specific pattern, to maintain durability and flexibility. Once the shell was done, the metal parts, such as inner threads or the gasoline cap housing, were glued in. One more fiber glass layer, hardening and hours of sanding. After that, painting prep and a visit of a paint shop. The cockpit is done and ready to be mounted.

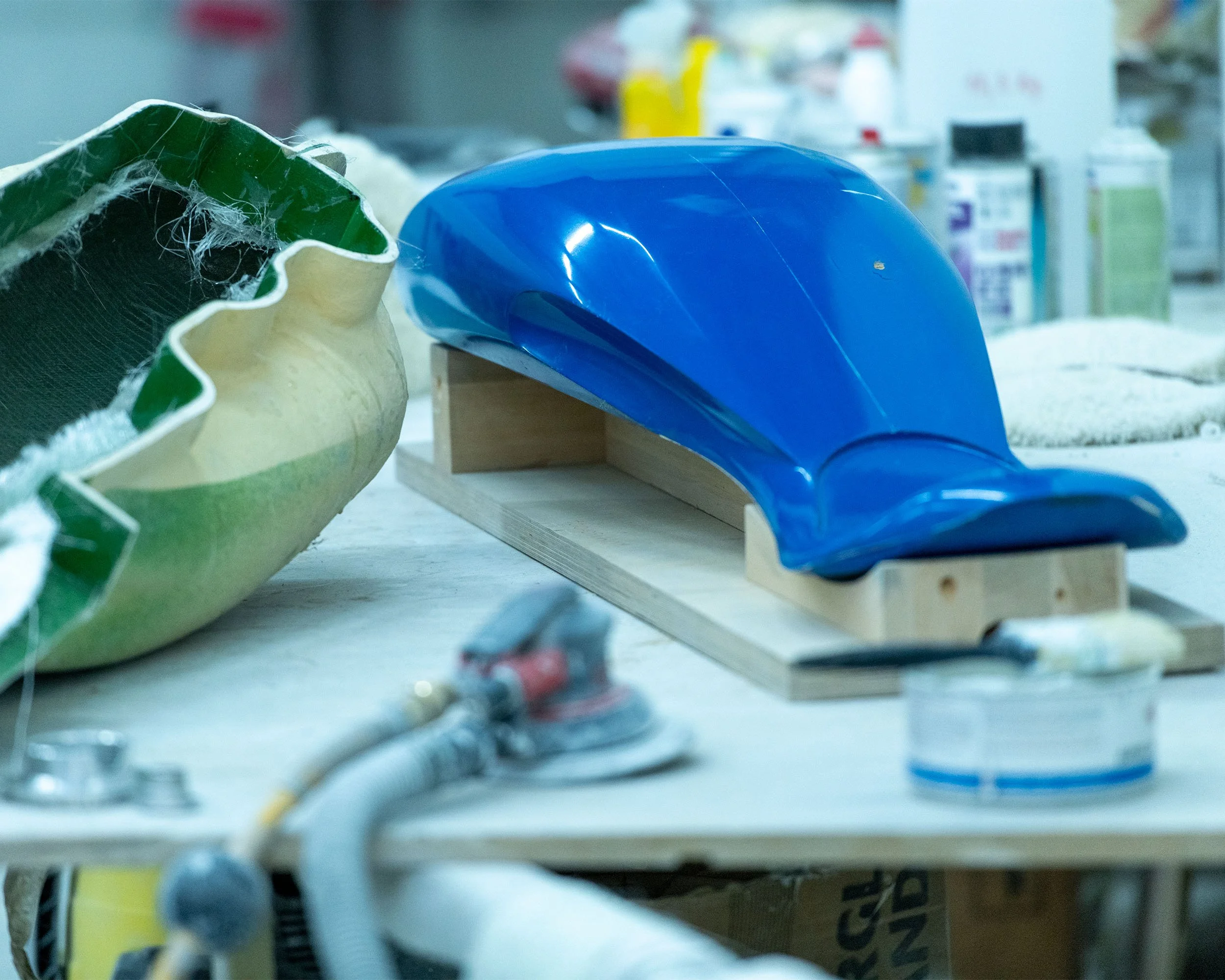
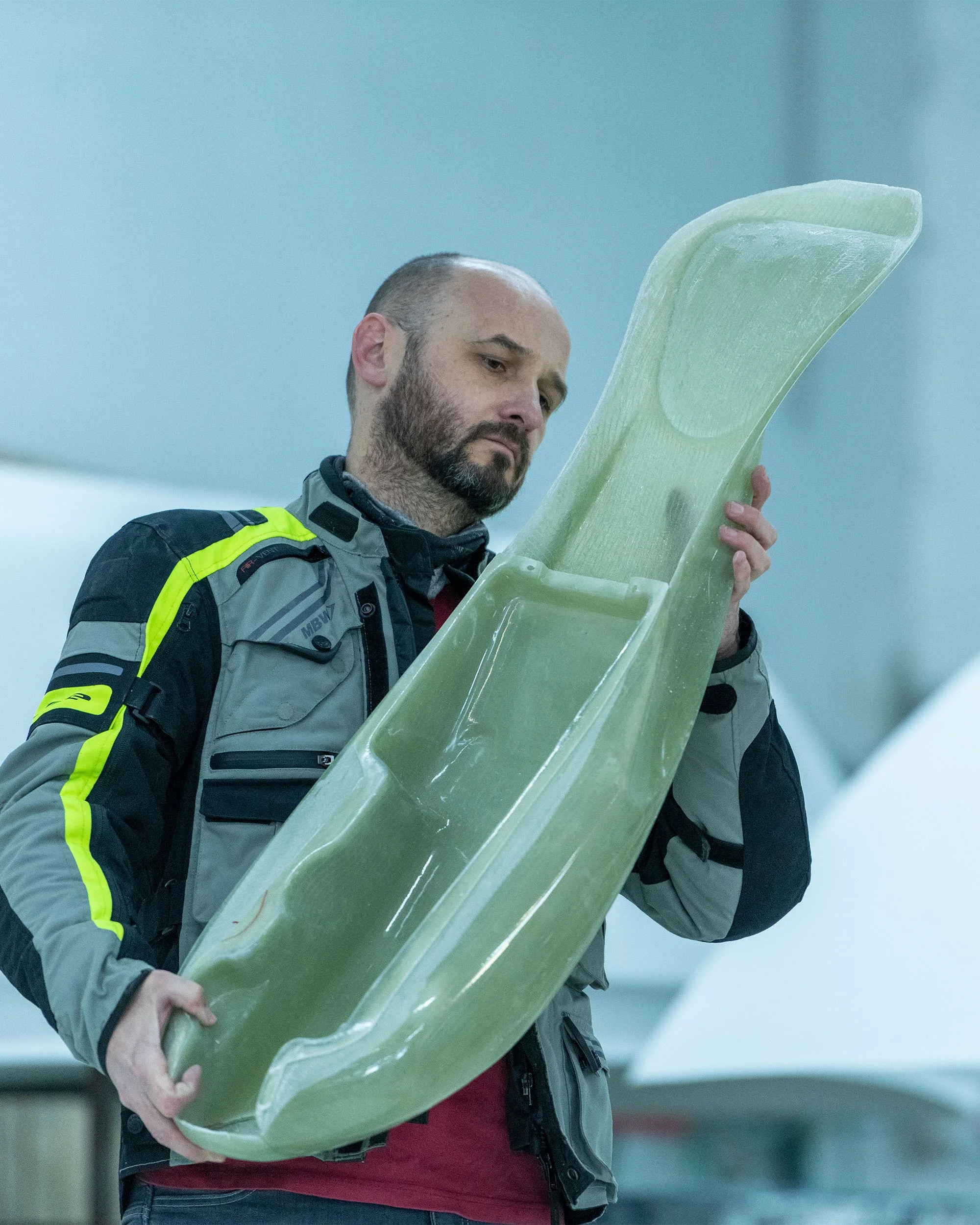



“A WINNER IS A DREAMER WHO NEVER GIVES UP.”
— Nelson Mandela —
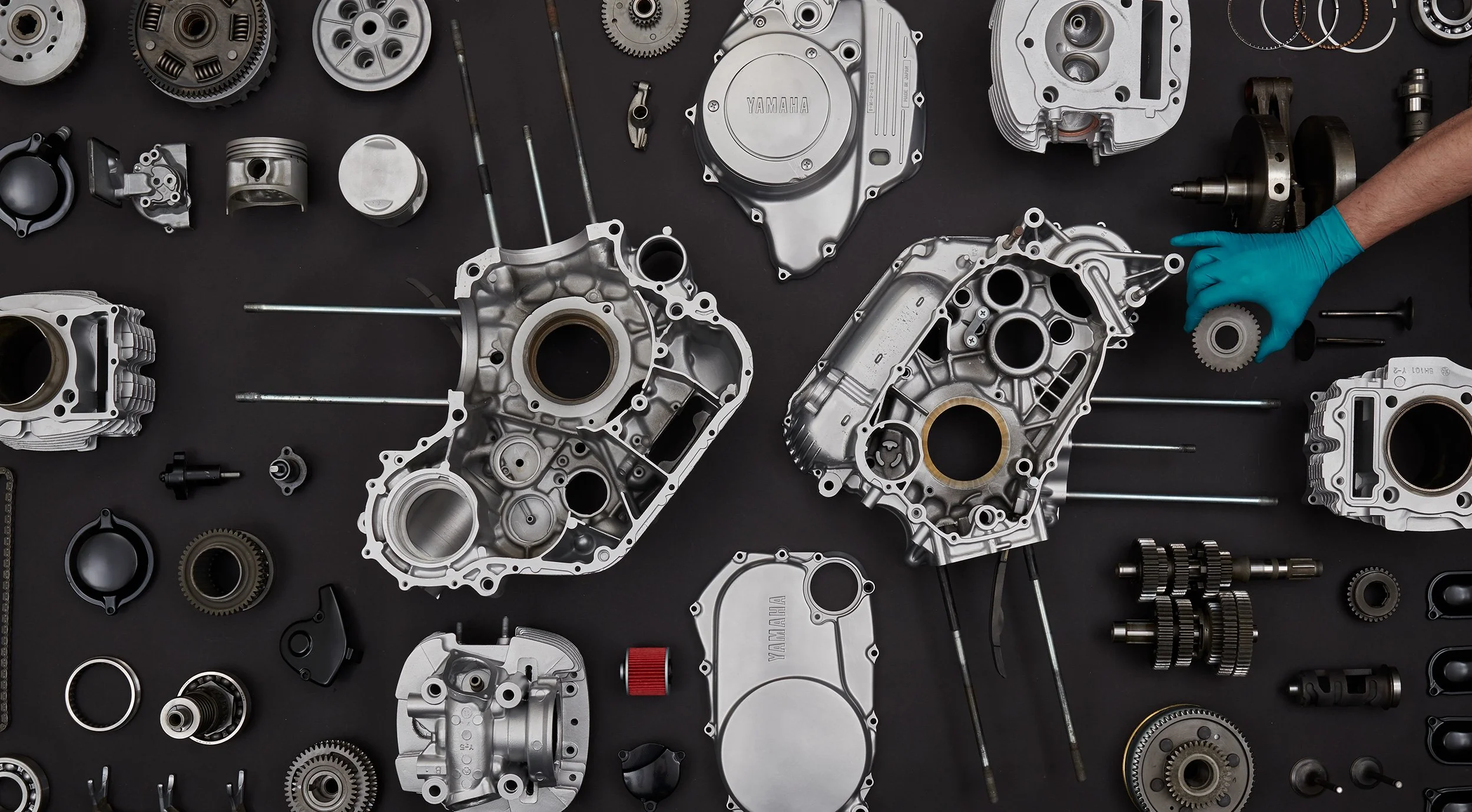
Just like with every engine in our workshop, also the XV920 was completely disassembled, cleaned, overhauled, painted and carefully assembled.

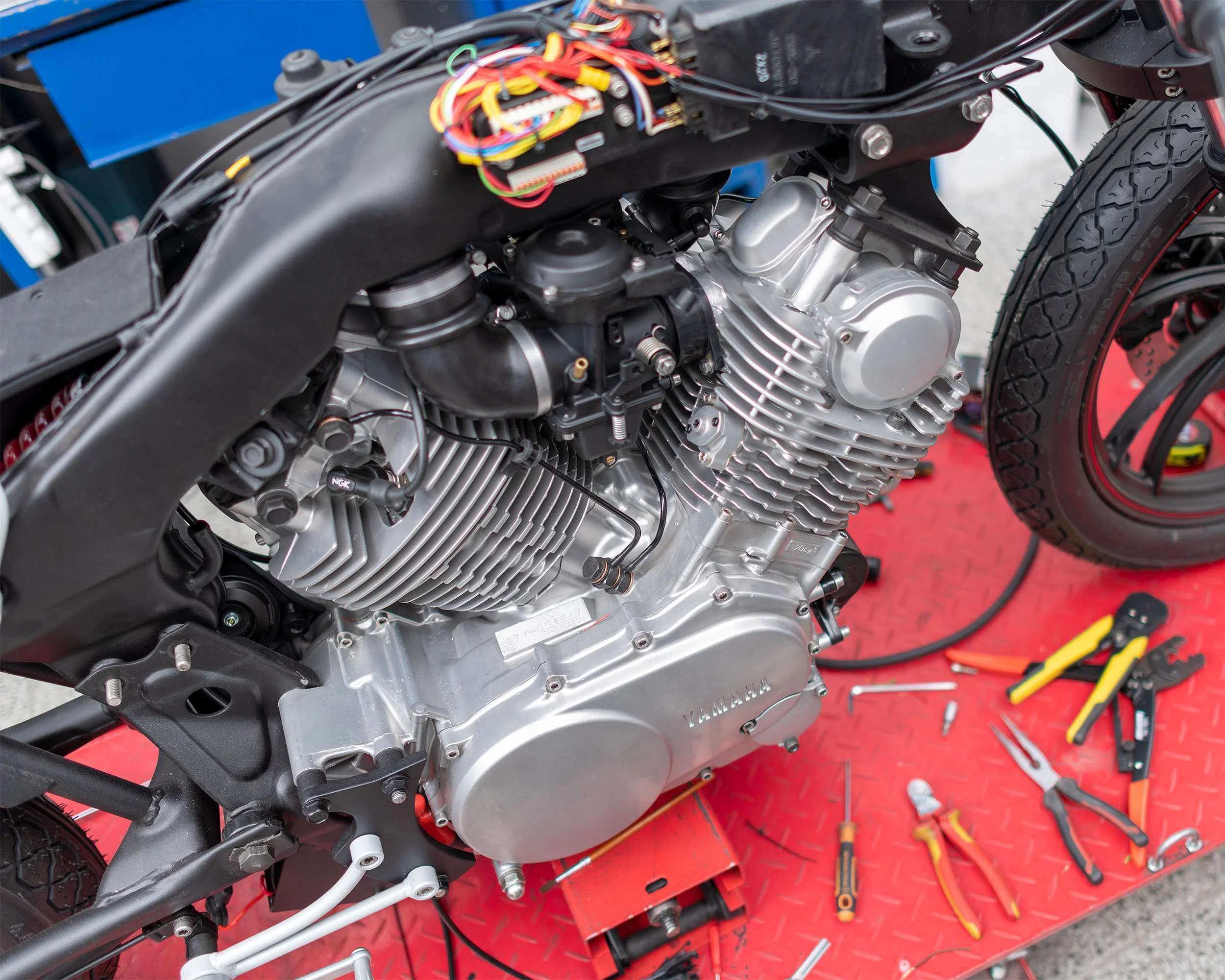
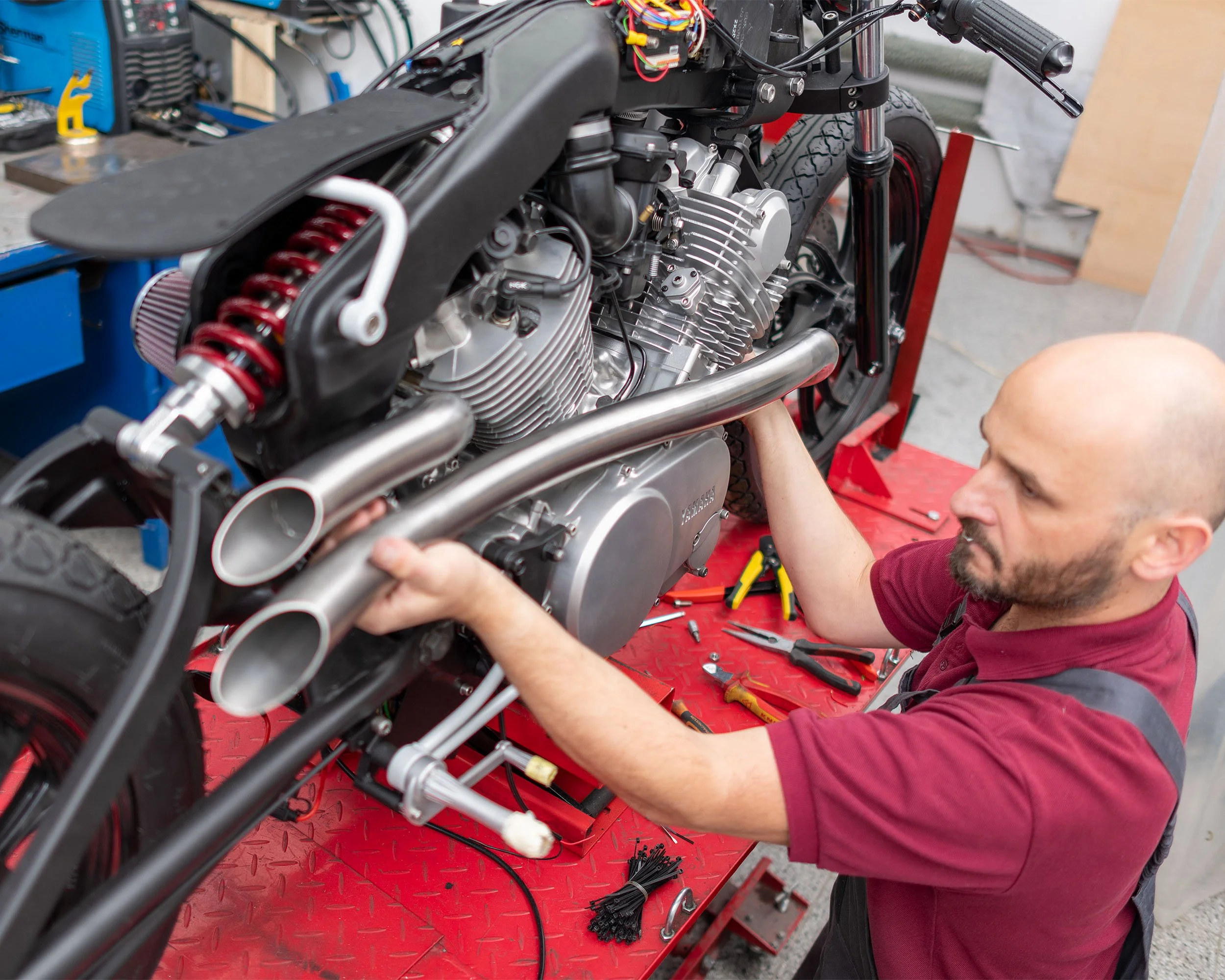

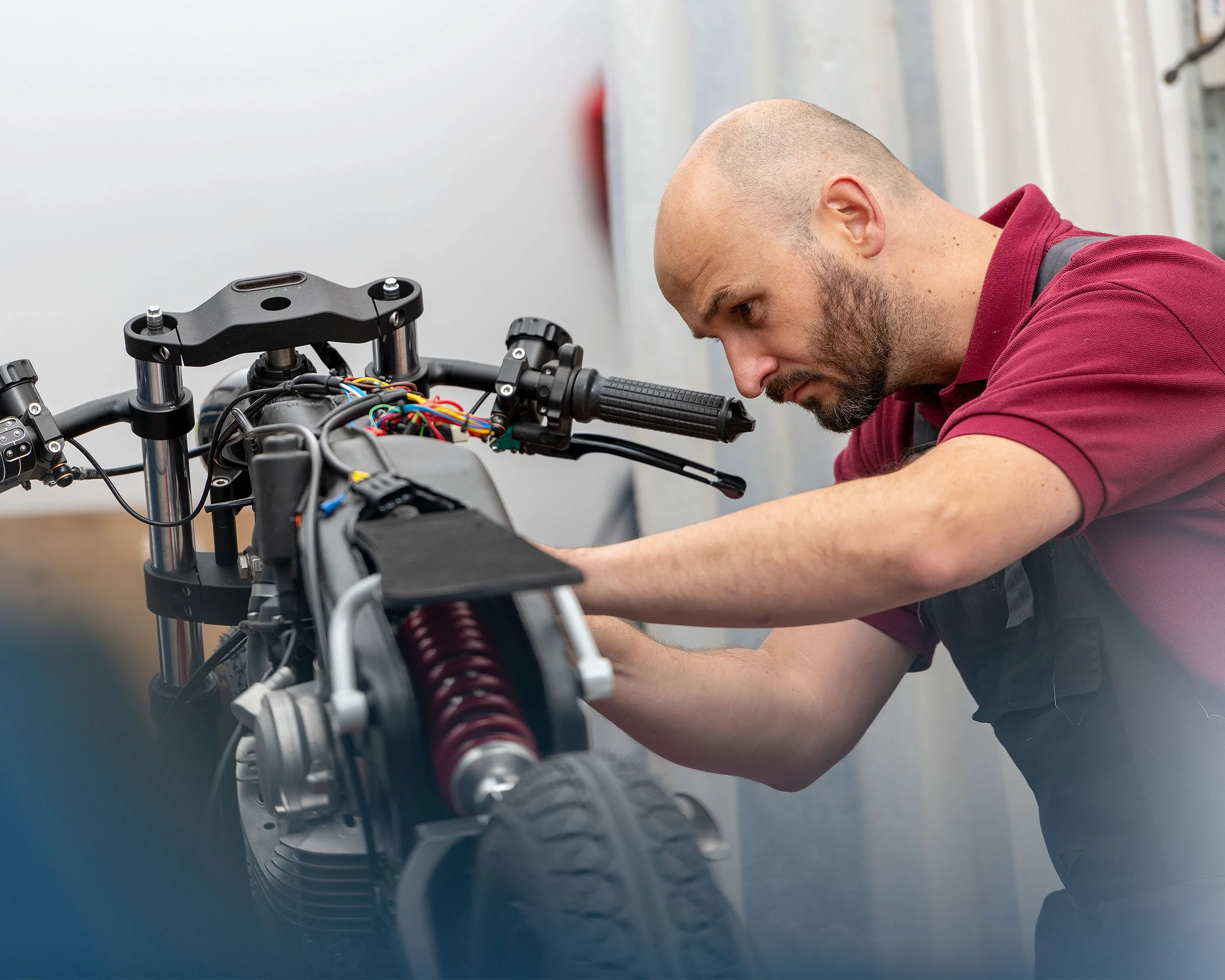
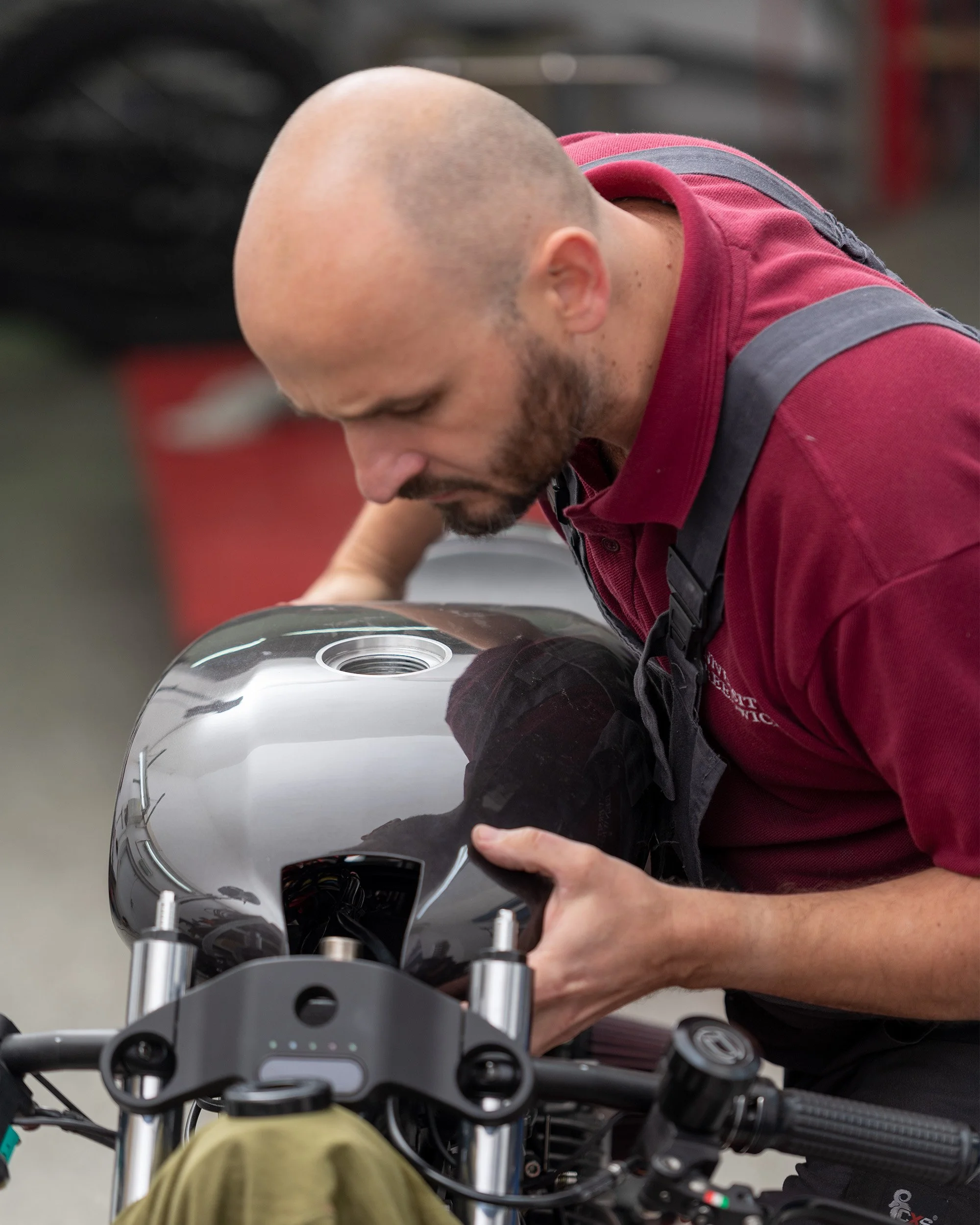
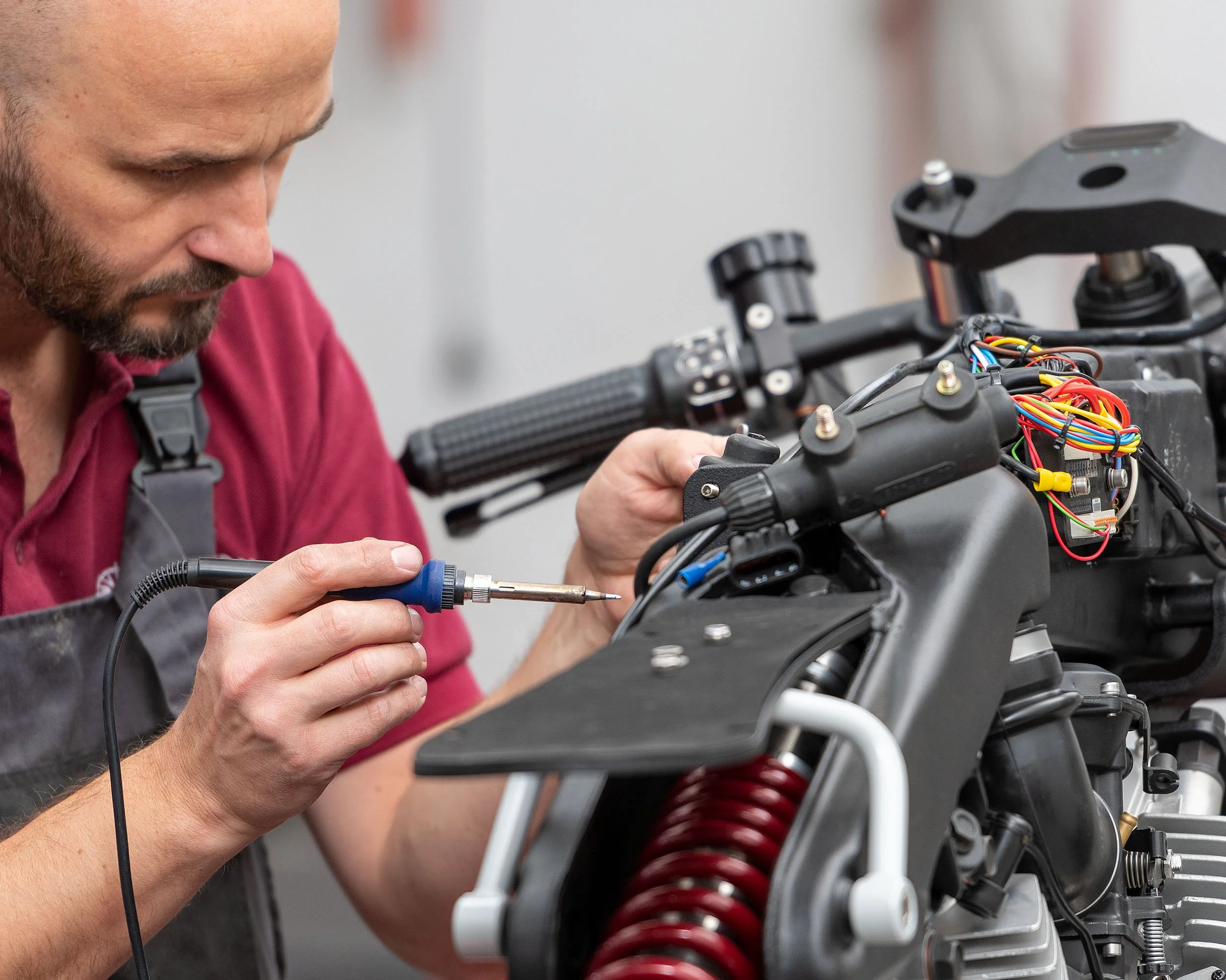
“HUMAN CRAFT AND HOURS OF PASSION GAVE BIRTH TO A UNIQUE BIKE, SOUNDING LIKE THUNDERSTORM AND FLOWING LIKE A FALCON IN THE AIR.”
— EARTH MOTORCYCLES —
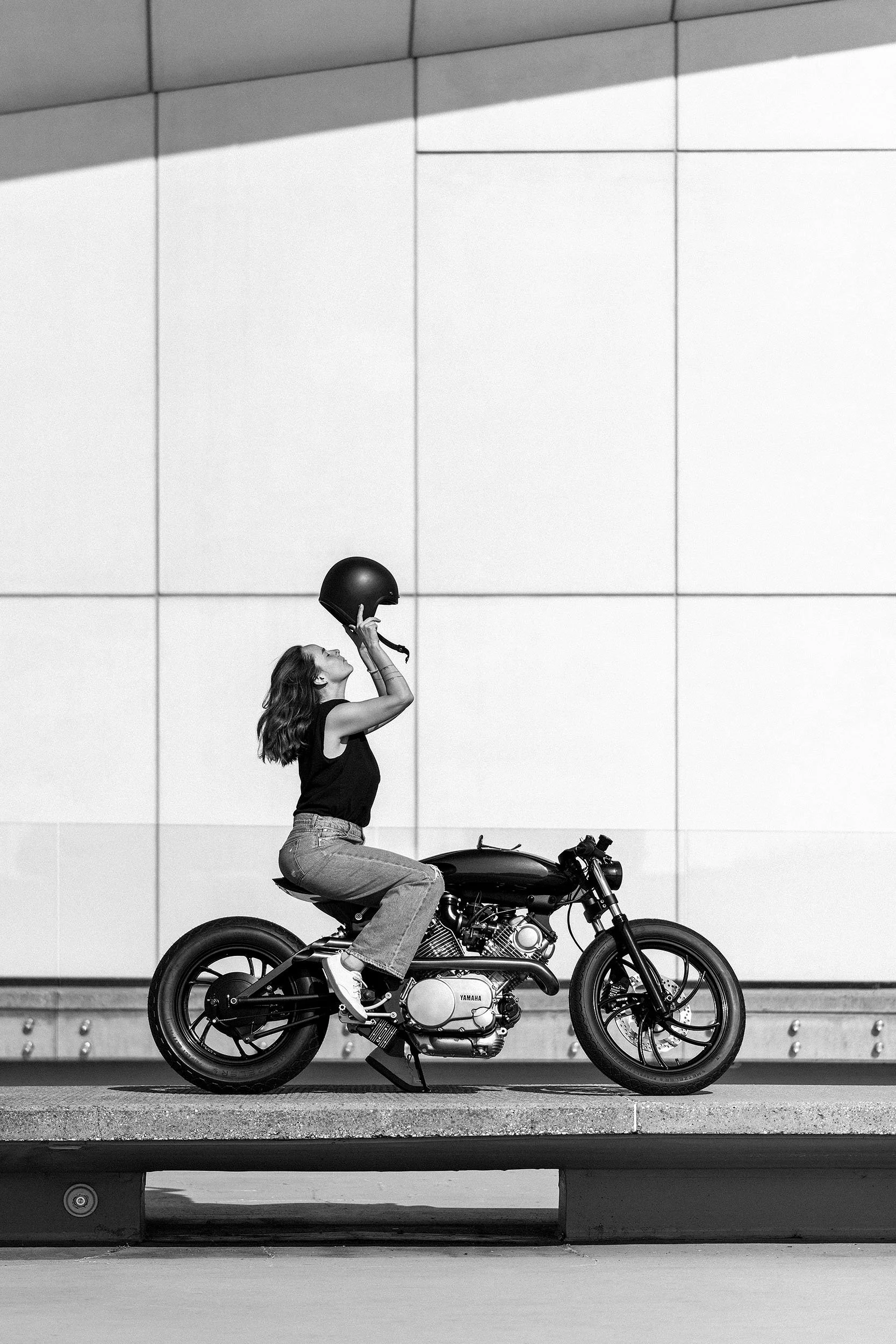